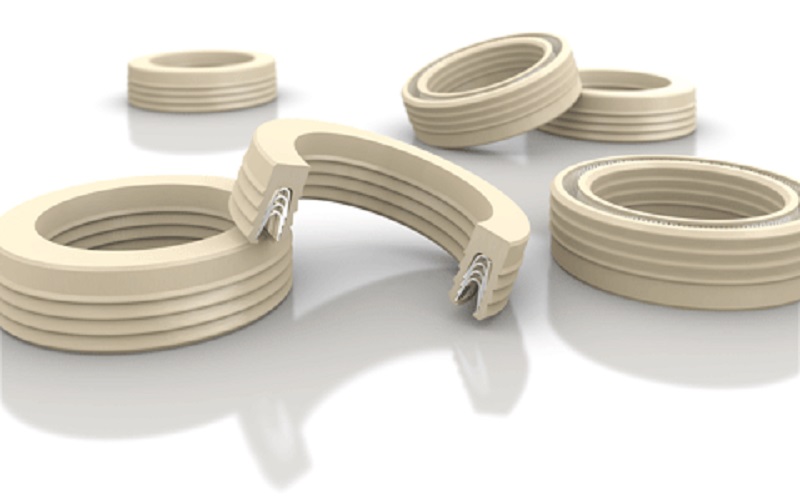
The Multi-Contact Turcon® Variseal® significantly improves sealing integrity and leak tightness
High Integrity Sealing Requirements
Trelleborg Sealing Solutions recommend the Multi-Contact Turcon® Variseal® when operational conditions require a subsea ball valve stem seal to perform with high resistance to chemical media, and under extreme temperatures whilst maintaining good extrusion or compression characteristics.
The Multi-Contact Turcon® Variseal® has been developed to replace multiple chevron seals or V-stack type products in subsea valve stems requiring a high-integrity sealing capability. It includes a series of single-acting spring-energized seals housed within a U-shaped Turcon® PTFE based material seal profile.
The unique single-piece design significantly improves sealing integrity and leak tightness in high-pressure applications by providing higher contact force across multiple seal hardware interfaces. It has been designed to provide integrated redundancy, helping to extend the flex life of seals in high-pressure applications while providing better performance and lower operator costs. With the addition of PEEK anti-extrusion devices, the Multi-Contact Turcon® Variseal® can withstand pressures of up to 207 MPa/ 30,000 psi.
Operational Pressure: |
30,000 psi / 207 MPa |
Speed: |
Up to 32 ft/s / 10 m/s |
Temperature Range: |
-320°F to +509°F -196°C to +265°C |
Clearance: | Typically up to 0.3mm at 2 MPa |
Media: |
Almost universal media compatability |
Design Considerations for Subsea Valve Stem Seals
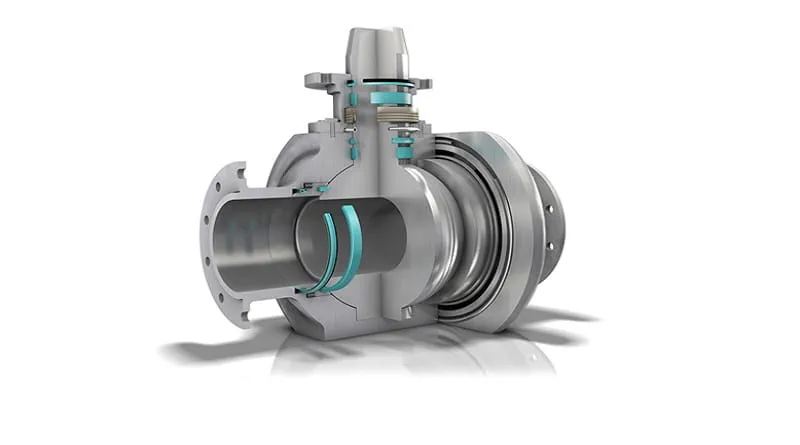
A subsea ball valve requiring a high integrity sealing solution
Valve design in general is a very broad subject, so in order to offer design considerations it is necessary to set some limits to the type of valves covered in this article. The subsea valve applications discussed herewith are Ball Valves, Gate Valves, Regulating Valves, Check Valves and Choke Valves.
There are typically three places in valves where seals are required; stem seals, seat ring seals and static seals (for covers and bonnets etc). The stem seal is located on the valve stem going out of the valve, and is used for operating the valve. The stem seal is to be considered as dynamic or semi-dynamic, with turning, reciprocating or helical movement.
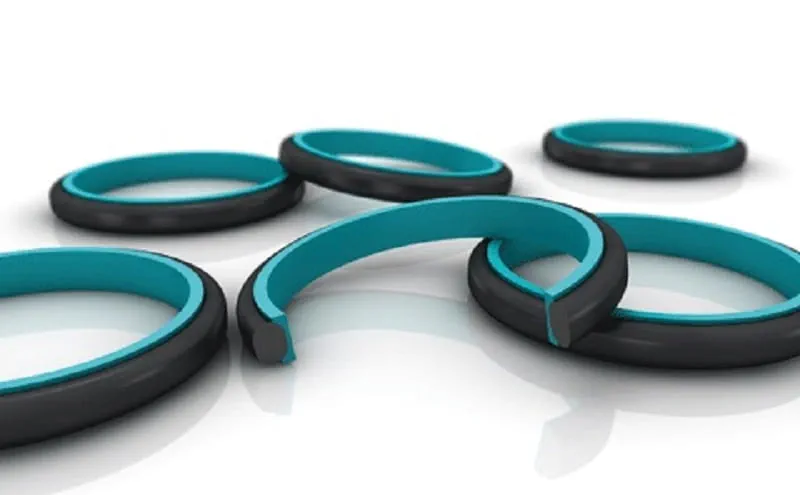
Turcon® Double Delta® is the original slipper seal developed to improve the performance of O-Rings and Back-up Rings
Differential Pressure Considerations
The stem seal is typically exposed to pressure coming from one side only, inside the valve. However, there are occasions (particularly within subsea use) where the differential pressure outside the valve could be as high or higher than the media pressure inside the valve. In situations like this it is important to consider the seal position when designing the valve stem arrangement. This can be done with one or more seals facing each direction, possibly with support rings in the spring grooves, to prevent seal damage in case of accidental back pressure.
If operating conditions permit it, bidirectional seals such as Turcon® Double Delta® can be used. Turcon® Double Delta® is the original slipper seal developed to improve the performance of O-Rings and Back-up Rings. It is a double-acting seal energized by an elastomer O-Ring. Demonstrating good friction properties, Turcon® Double Delta® provides stick-slip-free starting and excellent dry running.
Operational Pressure: |
5,000 psi / 35 MPa (15,000 psi / 103 MPa with Back-up Ring) |
Speed: |
Up to 50 ft/s / 15.0 m/s |
Temperature Range: Depending on elastomer material |
-49°F to +500°F -45°C to +260°C |
Clearance: |
As per AS568 and ISO 3601 seal sizes. Larger clearance possible with Back-up Ring |
Media: |
Mineral oil-based hydraulic fluids, flame-retardant hydraulic fluids, environmentally safe hydraulic fluids (bio-oils) Downhole fluids, water and others depending on the elastomer material selected Hydrocarbons, Sour Gas (including high concentrations), amines, acids & corrosion inhibitors, methanol |