Reduce FPSO Downtime and Easily Replace Large Diameter Seals In-situ with SealWelding™
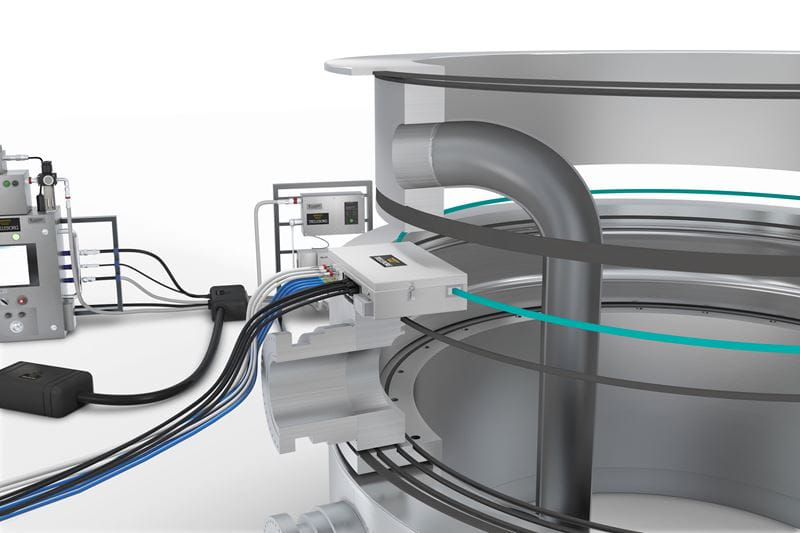
James Simpson, Global Segment Director Oil & Gas and Energy, Trelleborg Sealing Solutions, says: “Swivel stacks on FPSOs are large pieces of equipment that are difficult to maintain, with replacement of large diameter seals usually requiring the equipment to be returned to dock. This involves significant downtime and an extremely high cost in lost production. Our revolutionary SealWelding™ technology enables equipment operators to replace seals in the field without returning to shore while other stacks continue in operation. SealWelding™ is also a more sustainable option for the environment, as it reduces CO2 emissions that would otherwise be generated by the FPSO needing to sail back to port for repairs.”
A revolutionary process
The SealWelding™ process begins with production of a seal in a controlled manufacturing area at one of the Trelleborg Sealing Solutions global facilities. Manufacture of the seal is to the original specification, in its original material; a specially designed tool precisely cuts the seal. Offshore, onboard the FPSO, highly trained personnel from Trelleborg’s service team place the new seal, which has been cut in one place, into position. Using a specialized ATEX zone 1 certified fully enclosed welding machine, the two ends of the seal are joined together seamlessly. This enables other swivel stacks to continue production on the FPSO without risk. After completing the welding process, a Trelleborg expert polishes and checks the seal.
Safety is paramount
A control cabinet ensures the smooth running of the process, as well as monitoring and logging of all data. Providing the values from the recorded data are within set parameters, the seal receives a release certificate showing it is ready for operation.
Simpson continues: “We are confident that our fully tested and portable system not only makes life for the offshore operator safer and easier, but also dramatically improves the bottom line for the oil company.”
A collaborative approach
Typically organized into three phases, a SealWelding™ project starts with a kickoff meeting and site survey, followed by building and validation of equipment and tools, and ends with offshore welding that includes mounting the seal into the swivel. This approach has so far helped clients worldwide and is beneficial in large seal applications subject to costly downtime, such as seen in the oil and gas, wind, and hydro power industries.
>>Find out more about SealWelding™ technology
>>Watch our YouTube video
Technical webinar
Join Technical Manager, Henk-Willem Sanders, for an in-depth look at how SealWelding™ technology can minimize costly equipment downtime